Reelvision delivers plastic-free carton for clinical trial facility
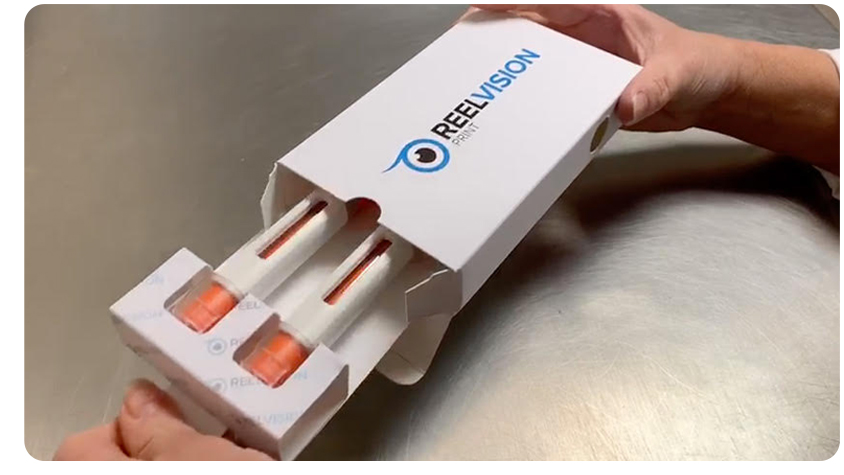
Reelvision Print is helping a pharmaceutical clinical trial company to reduce its environmental footprint by taking the plastic out of its secondary packaging.
We recently fulfilled an order for 7,500 cardboard cartons with bespoke fitment for two large, needle-free syringe. Traditionally this fitment would be made from plastic, but the client specifically asked our team to design a cardboard alternative.
This project is one of the latest in a series of packaging solutions created by Reelvision for the clinical trial facility where studies support pharmaceutical companies in the pursuit of potentially life-changing and life-saving medications.
Changing the way that syringes and other clinical components such as ampoules, bottles and vials are packaged and reducing waste is part of the client’s wider corporate responsibility and sustainability strategy. At Reelvision Print we share a similar commitment to reducing our environmental impact as our Managing Director Gareth Bakewell explains:
“All our paperboard comes from a sustainable source. For every tree cut down, our supplier ensures that at least three new ones are planted. This approach means that growth is always greater than the harvested volume.”
“On our production line, waste fibre board material is automatically removed and stored prior to being channelled into the recycling process,” he adds.
As well as being environmentally friendly, cardboard fitments are also more cost-effective than plastic fitments. This is another important consideration for our clients in clinical trial market where the majority of secondary (or outer) packaging is not branded and for single use only with the priority being on protecting the investigational medicinal product.
To ensure our bespoke packaging solution for the two needle-free syringes was fit for purpose, we firstly created a prototype using our inhouse CAD (Computer Aided Design) unit and technical drawings of the injectors supplied by the client. Following approval of this prototype and the creation of detailed specifications, Reelvision Print manufactured all packaging components within a ten-day lead time and arranged delivery on a direct door to door transportation service.
Reelvision Print MD, Gareth Bakewell, concludes: “Our state-of-the-art one-pass printing process, combined with our team’s passion and attention to detail, allows us to guarantee a rapid, reliable and flexible service. All our production complies with the ISO9001:2015 quality management standard and PS9000:2016 pharmaceutical good manufacturing practice, further adding to the assurances we offer to our customers in the pharmaceutical industry.”